Forschungsprojekt
CoBot-basierte Pick-and-Place-Anwendung
Umsetzung einer Produktionsanlage mittels kollaborativem Roboter für das Handling von Gehäusedeckel zur Zuführung in eine Bedruckungsstation
zurück zur Übersicht Projektliste
Im Produktionsprozess der Firma Belimo Automation AG wurden Gehäusedeckel bisher ausschliesslich händisch von der Anlieferungskiste auf eine Druckstation zur Beschriftung zugeführt. Weil es sich dabei um einen repetitiven und ressourcenintensiven Arbeitsschritt handelt, stellte sich bei Belimo die Frage: Könnte das Handling der Gehäusedeckel durch einen kollaborativen Roboter übernommen werden?
»Video "CoBat-basierte Pick-and-Place-Anwendung"
Das Bedrucken von Gehäusedeckeln im Produktionsprozess der Firma Belimo benötigte bisher einen Mitarbeitenden, der von Hand die Gehäusedeckel in der Anlieferungskiste greift, auf der Druckstation platziert und danach in einer weiteren Kiste für die Weiterverarbeitung ablegt. Der Arbeitsschritt ist repetitiv und ressourcenintensiv. Daher beauftragte Belimo das ILT Institute for Lab Automation and Mechatronics die Übernahme dieses Arbeitsschrittes durch einen kollaborativen Roboter zu klären.
Aus Sicht der Robotik handelt es sich auf den ersten Blick um eine Standard Pick'n Place-Anwendung unter Einbezug eines Bildverarbeitungssystems. Die engen Platzverhältnisse in den Kisten und die Gegebenheit, dass die Gehäusedeckel lose angeliefert werden und bei angebrochenen Kisten auch ungeordnet liegen können, verleihen der Aufgabe jedoch einen hohen Komplexitätsgrad.
In einem ersten Schritt wurde die Eignung der Applikation für den Einsatz eines kollaborativen Robotersystems beurteilt. Dabei standen die, für den Prozess, relevante Kriterien, wie erforderliche Bewegungsabläufe des Roboterarms sowie Prozess- und Sicherheitsaspekte im Zentrum der Betrachtung. Auch wurden die erforderlichen Interaktionen zwischen Roboter und Bediener ausfindig gemacht und beurteilt. Da es sich bei der Teilebedruckung um einen Offline-Prozessschritt handelt und somit ein Eingreifen vom Bediener in den Prozess nicht zu Verzögerungen in der Produktionskette führt, kommt dem Einsatz eines kollaborativen Roboters zudem entgegen.
Bei der Konzipierung wurden Fragen zum konkreten Aufbau der Anlage, wie z.B. welcher kollaborative Roboter eignet sich für die Applikation und bietet zudem ein gutes Preis- / Leistungsverhältnis sowie welches Kamerasystem erfüllt die gestellten Anforderungen zur Erkennung der verschiedenfarbigen Gehäusetypen, geklärt. Die Vor- und Nachteile der unterschiedlichen Systeme wurden gegeneinander abgewägt und daraus der Konzeptentscheid für die Umsetzung, mittels UR5e von Universal Robots und einem InSight 7905M Vision System von Cognex, gefällt.
Bei der anschliessenden Realisierung zeigten sich die Herausforderungen komplexer CoBot-Applikationen und den daraus resultierenden erhöhten Anforderungen an die Programmierung. So musste z.B. ein Grossteil der Roboter-Programmierung in den erweiterten Script-Funktionen umgesetzt werden, da die benötigte Funktionalität durch die Standardprogrammierung nicht vollends abgedeckt werden konnte. Aufgrund der Limitierungen der Roboterkinematik musste zudem eine siebte Achse an der Greifperipherie implementiert werden, damit eine rasche Umorientierung für das Einlegen der Gehäuseteile für die Bedruckung gewährleistet werden konnte.
Für die Interaktion zwischen Roboter und Bediener wurden zusätzliche cobot-spezifische Features, wie z.B. eine sensitive Füllstanderkennung mittels tasten in der Kiste, in den Programmablauf implementiert. Weiter wird jeweils der erste bedruckte Gehäusedeckel eines neuen Druckauftrages dem Bediener zur Kontrolle präsentiert. Bei zufriedenstellendem Druckresultat kann durch leichtes seitliches Anschieben an der Greifperipherie der CoBot zum Ablegen des Gehäusedeckels in die Ausgangskiste aufgefordert werden. Ist das Druckresultat ungenügend kann der Gehäusedeckel händisch vom Greifer abgezogen werden und der Prozess startet von Neuem. Zur Steigerung der Benutzerfreundlichkeit wurden zudem die Standard-Bedienelemente auf dem UR-Panel mit einer zusätzlichen kundenspezifische Bedienoberfläche basierend auf UR-Caps erweitert. Die Anlage ist heute im produktiven 3-Schicht Betrieb im Einsatz und unterstützt die Menschen bei repetitiven Aufgaben.
"Die Taktzeiten sind im Vergleich zum Menschen zwar länger, dennoch sind wir mit dem Resultat sehr zufrieden", sagt Beat Kirchhofer, Head of Production Engineering bei BELIMO Automation AG. "Der CoBot arbeitet kontinuierlich und muss nur ab und zu mit Material versorgt werden. Durch das Projekt mit dem ILT haben wir einen Eindruck gewonnen, in welchen Anwendungsfällen CoBots geeignet sein können. Ideen für weitere Anwendungen können nun aufgrund der Erfahrungen einfacher bewertet werden. Die Zusammenarbeit mit dem ILT war erfolgreich, weil die dort vorhandenen Erfahrungen ins Projekt einfliessen konnten und weil wir eine sehr unkomplizierte und schlanke Art der Zusammenarbeit etablieren konnten."
Projektverantwortlicher
Daniel Felder
ILT Institut für Laborautomation und MechatronikBereichsleiter Mechanical Engineering, BSc FHO in Maschinentechnik
+41 58 257 47 29daniel.felder@ost.ch
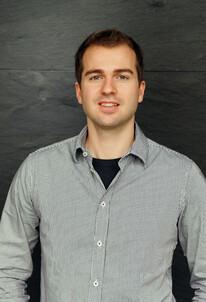
Beteiligte Institute
ILT Institut für Laborautomation und Mechatronik
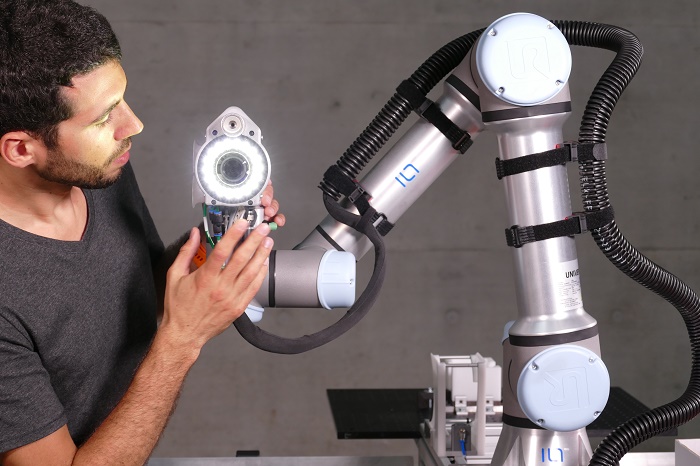
